Industrial Safety
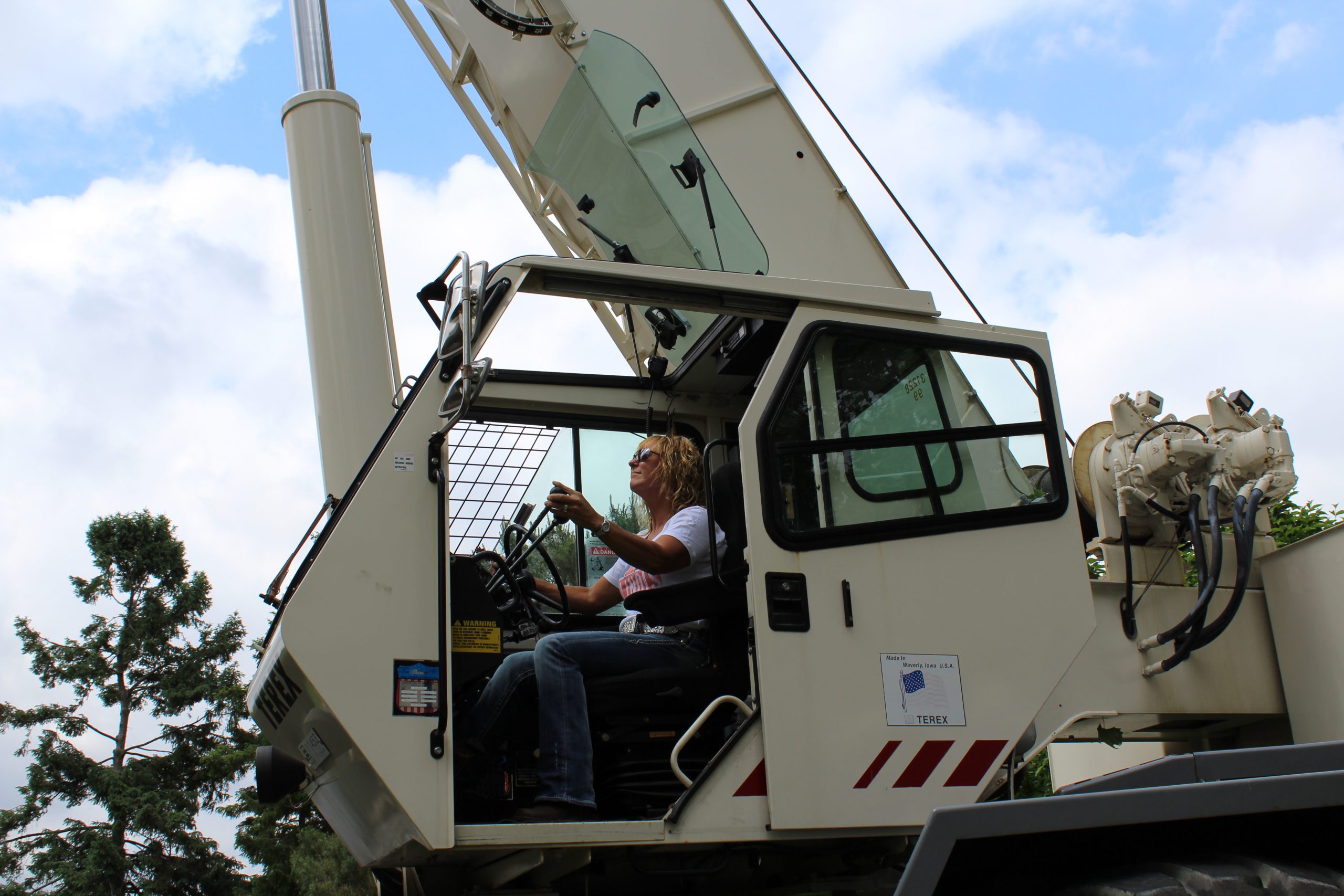
Industrial safety encompasses many of the professional occupations on campus. In addition to the maintenance and construction workers involved in heavy industrial work, many other employees, faculty, and students routinely or occasionally perform work that exposes them to industrial hazards. The programs listed on the left provide information and resources for some of the industrial safety issues facing campus workers.
Many of the buildings on campus were constructed before federal regulations were passed prohibiting the use of some asbestos-containing materials. This section outlines the information, services, and consulting provided by Occupational Safety and Health Department to promote a campus environment that protects students, faculty, and staff from contact with asbestos fibers.
For additional information contact the Division of Safety and Compliance at 217-265-9828, or safetyandcompliance@illinois.edu.
Asbestos Hazard Emergency Response Act (AHERA) Work Permits
All non-asbestos maintenance and construction work in Asbestos Hazard Emergency Response Act (AHERA) designated buildings must be performed under an AHERA Work Permit. Individual building permits are available for use by Facilities & Services and Technology Services employees. A consolidated permit has been created for use by contractors. Permits must be filled out before work begins and must be available at the job site throughout the duration of the work. Once work is complete, completed work permits must be provided to the Division of Safety and Compliance via email at oshs@illinois.edu or a hard copy placed in the hanging file folder across from the Tool Room in the Physical Plant Service Building.
PURPOSE
The University of Illinois Urbana-Champaign, through the division of Safety and Compliance, Occupational Safety and Health (OSH) department, has established this Confined Space Entry Program to protect the health of university students, faculty and staff and to assure compliance with state and federal occupational safety and health standards.
This program provides the minimum requirements for unit-specific confined space entry programs. It is expected that campus units will utilize this Confined Space Entry Program to develop unit-specific standard operating procedures (SOPs), including completion of Appendix A and providing the first page to OSH.
RESPONSIBILITIES
Occupational Safety and Health (OSH)
OSH is responsible for the administration of this program. OSH maintains copies of all records for services provided by OSH pertaining to this program. An OSH program coordinator is designated to provide guidance, regulatory interpretation, and oversight for this program and to review this program annually.
Deans, Department Heads, and Directors (Campus Units)
Campus units shall provide the resources necessary to properly implement this program and unit-specific SOPS (Appendix A) and designate a responsible person that will be charged with implementing this program and unit-specific SOPs.
Campus Unit Responsible Person
The responsible person shall work with campus unit supervisors to identify personnel that may be required to participate in confined space entry operations, ensure that personnel attend appropriate training before entering a confined space, and ensure that unit-specific SOPs (Appendix A) are reviewed annually.
Supervisors of Confined Space Entry Operations Personnel (Supervisors)
Supervisors and Principle Investigators (PIs) are responsible for enforcement of this program and unit-specific SOPs (Appendix A). They shall assist in the development and annual review of unit-specific SOPs, and ensure that their employees affected by confined space receive appropriate training.
Confined Space Entry Operations Personnel
Affected faculty, staff, and students, herein called confined space entry operations personnel, are responsible for adhering to the provisions of this program, unit-specific SOPs (Appendix A), and manufacturer instructions.
PROCEDURES
Entry Permit System
Before entry is allowed into a permit-required confined space, the entry supervisor shall obtain and complete Appendix D – Confined Space Entry Permit. Upon completion of this permit, the entry supervisor shall sign it to allow entry. The completed permit shall be made available to all authorized entrants or their representative by posting it at the entrance of the confined space or via some other effective means.
Entry Procedures
Each campus unit shall develop procedures for entry into their permit-required confined spaces.
Entry Equipment
Campus units must provide the equipment necessary to safely enter a permit space as well as training necessary to ensure the equipment is used properly at no cost to affected employees. Campus units are also responsible for ensuring proper maintenance of the equipment.
Communication and Coordination
Whenever entry into a permit space is performed on campus by contractor personnel a pre-entry meeting must occur between a representative of the campus unit that controls the space and the controlling contractor. Information on permit space locations, known and potential hazards, and means of eliminating or controlling hazards shall be discussed.
A post-entry debrief must also occur whereby the controlling contractor communicates to the campus unit representative on the permit spaces entered, the program followed, and hazards confronted and created during entry operations.
Campus unit personnel who perform entry operations into spaces owned by others would be considered a controlling contractor during entry operations. The unit confined space entry supervisor must participate in pre- and post-entry meetings with a representative of the host employer and cover topics discussed immediately above.
Non-Entry Rescue
Non-entry rescue is required unless the retrieval equipment would increase the overall risk of entry or would not contribute to the rescue of the entrant.
Rescue and Emergency Services
Rescue services must be provided and they must be able to respond to an incident on any shift within four minutes. The rescue services for the Urbana campus locations are the Champaign Fire Department and Urbana Fire Department depending upon your location on campus. The appropriate fire department should be contacted prior to entry into a permit space.
Appendices:
Useful Resources:
OSHA 1926 Subpart AA Confined Spaces in Construction Standard
The Lockout-Tagout (LOTO) Program provides detailed information on how energy sources must be locked and tagged out before employees perform any servicing or maintenance activities where the unexpected energizing, start-up, or release of stored energy could cause injury.
PURPOSE
The University of Illinois Urbana‐Champaign, through the Facilities and Services Division of Safety and Compliance, Occupational Safety and Health Department (OSH), has established this Control of Hazardous Energy Program to protect the health of university students, faculty and staff and to assure compliance with State and Federal occupational safety and health standards.
This Program provides the minimum requirements for unit‐specific control of hazardous energy programs. It is expected that campus units will utilize this Control of Hazardous Energy Program to develop unit‐specific standard operating procedures (SOPs) including completion of Appendix A ‐ Unit‐Specific Standard SOPs and providing the first page to OSH.
RESPONSIBILITIES
Occupational Safety and Health (OSH)
OSH is responsible for the administration of this Program. OSH maintains copies of all records for services provided by OSH pertaining to this Program. An OSH program coordinator provides guidance, regulatory interpretation and oversight for this Program and reviews this Program annually.
Deans, Department Heads, and Directors (Campus Units)
Campus Units shall provide the resources necessary to properly implement this Program and Appendix A‐Unit‐Specific SOPs, and designate a Responsible Person that will be charged with implementing this Program and Appendix A ‐ Unit‐Specific SOPs.
Campus Unit Responsible Person
The Responsible Person shall work with Campus Unit Supervisors to identify personnel that may be required to repair or maintain equipment and machines having sources of hazardous energy, ensure that personnel attend appropriate training before performing work that could result in an expected startup or energization of hazardous energy sources, and ensure that the Appendix A ‐ Unit‐Specific SOPs are reviewed annually.
Supervisors for Personnel Applying Energy Control Locks and Tags (Supervisors)
Supervisors and Principle Investigators (PIs) are responsible for enforcement of this Program and Appendix A ‐ Unit‐Specific SOPs. Supervisors and Principle Investigators (PIs) are responsible for ensuring development of equipment‐specific procedures for equipment and machines for which they have responsibility. They shall assist in the development and annual review of Appendix A ‐ Unit‐Specific SOPs, ensure annual audits are performed for the personnel and equipment/machines they have responsibility for, and ensure that their employees receive appropriate training.
Personnel Applying Energy Control Locks and Tags
Faculty, staff and students who apply energy control locks and tags are responsible for adhering to the
provisions of this Program, Appendix A ‐ Unit‐Specific SOPs, and manufacturer instructions. They must
only apply locks and tags to equipment/machines for which they have been authorized by their
supervisor and trained to service or maintain. They shall participate in annual audits as directed by their
supervisor or the Campus Unit Responsible Person. They shall follow equipment‐specific energy control
procedures or develop them when none exist. The Appendix C ‐ Example Equipment‐Specific Energy
Control Procedure Form can be used to document procedures for Campus Unit equipment.
PROCEDURES
Equipment‐Specific Energy Control Procedures
An equipment‐specific procedure is not required when ALL of the following exist:
- The machine or equipment has no potential for stored or residual energy or reaccumulation of stored energy after shut down which could endanger employees;
- The machine or equipment has a single energy source which can be readily identified and isolated;
- The isolation and locking out of that energy source will completely de‐energize and deactivate the machine or equipment;
- The machine or equipment is isolated from that energy source and locked out during servicing or maintenance;
- A single lockout device will achieve a locked out condition;
- The lockout device is under the exclusive control of the Authorized Employee performing the servicing or maintenance;
- The servicing or maintenance does not create hazards for other employees; and
- The Campus Unit, in utilizing this exception, has had no accidents involving the unexpected activation or reenergization of the machine or equipment during servicing or maintenance.
Specific procedures must be developed for each piece of equipment, or for each class of related equipment.
Program Evaluation
This Program will be reviewed annually by OSH. The written Appendix A ‐ Unit‐Specific SOPs and associated records shall be reviewed and updated by the respective Campus Unit at least annually and more frequently as hazards, tasks, procedures and/or equipment change. Annual Campus Unit reviews shall be recorded and kept on file using Appendix I ‐ Program Audit Checklist.
Appendices:
PURPOSE
The University of Illinois Urbana-Champaign (University), through the Division of Safety and Compliance, Occupational Safety and Health Department (OSH), has established this Crane and Hoist Safety Program to protect the health of university students, faculty and staff and to promote compliance with State and Federal occupational safety and health standards.
This Program establishes the minimum requirements for unit-specific crane and hoist work practices and inspection procedures. It is expected that campus units will utilize this Program to develop unit-specific standard operating procedures (SOPs) including completion of Appendix A Unit-Specific SOPs and providing the first page to OSH.
RESPONSIBILITIES
Occupational Safety and Health (OSH)
OSH is responsible for the administration of this Program. OSH maintains copies of all records for services provided by OSH pertaining to this Program. An OSH program coordinator provides guidance, regulatory interpretation and oversight for this Program and reviews this Program annually.
Deans, Department Heads, and Directors (Campus Units)
Campus Units shall provide the resources necessary to properly implement this Program and designate a Responsible Person that will be charged with implementing this Program.
Campus Unit Responsible Person
The Campus Unit Responsible Person shall ensure that any crane and hoist within their area of responsibility is inspected by a factory-trained employee or qualified contractor as specified in the Periodic Inspections section below.
Supervisors of Affected Employees (Supervisors)
Supervisors and Principle Investigators (PIs) are responsible for enforcing proper work practices under their responsible charge in accordance with this Program and unit-specific SOPs. They shall ensure that all of their personnel who may operate or work around cranes and hoists receive appropriate training.
Operators of Cranes and Hoists (Competent Operators)
Competent Operators shall:
- Attend training on and follow the requirements of this Program;
- Only operate cranes and hoists that they have trained on;
- Follow all crane and hoist operating procedures;
- Conduct the appropriate inspections when they are required and complete the required documentation as necessary;
- Notify the supervisor of any deficiencies identified during inspections and report all incidents involving cranes and hoists to supervisors immediately; and
- Maintain full attention on the task being performed (e.g., no use of headsets, music).
PROCEDURES
General
- Equipment shall only be operated by a Competent Operator or trainee that is under the direct supervision of the Competent Operator.
- No personnel shall be allowed to walk or be under a suspended load.
- All employees who handle wire slings and hoist cables shall wear leather gloves to prevent hand injuries.
- Proper guards must be in-place for exposed gears, belts, electrical equipment, couplings and fans.
- Suspended loads shall be kept clear of all unnecessary obstructions and personnel.
- Hands and fingers shall not be placed between the sling and its load while the sling is being tightened around the load.
- Shock loading is prohibited.
- A sling shall not be pulled from under a load when the load is resting on the sling.
Program Evaluation
This Program will be reviewed annually by OSH. The written Unit-Specific SOPs shall be reviewed and updated by the respective Campus Unit at least annually and more frequently as hazards, tasks, procedures and/or equipment change.
Appendices:
Electricity-related hazards include electric shock and burns, arc-flash burns, arc-blast impacts, and falls – all of which can be fatal. Precautions including proper training, electrical rated personal protective equipment, and establishing minimum approach distance must be taken when working on or around exposed live electrical hazards.
OSHA Working Safely with Electricity Fact Sheet
For additional information contact the Division of Safety and Compliance at 217-265-9828, or safetyandcompliance@illinois.edu.
The Occupational Safety and Health Administration (OSHA) requires trench protection in all excavations and trenches deeper than 5 feet. However, even in excavation and trenches less than 5 feet deep, trench protection may be required depending on the soil type and presence of water.
The Facilities & Services tool room has several systems designed to protect workers from accidental cave-ins.
For additional information or assistance contact the Division of Safety and Compliance at 217-265-9828 or safetyandcompliance@illinois.edu.
PURPOSE
The University of Illinois Urbana-Champaign, through the Division of Safety and Compliance, Occupational Safety and Health Department (OSH), has established this Elevated Work Program to protect the health of university students, faculty and staff and to assure compliance with State and Federal occupational safety and health standards.
This Program provides the minimum requirements for unit-specific elevated work procedures. It is expected that campus units will utilize this Elevated Work Program to develop unit-specific standard operating procedures (SOP).
RESPONSIBILITIES
Occupational Safety and Health (OSH)
OSH is responsible for the administration of this Program, which includes general awareness training, assisting in the identification of fall hazards, and assisting in the selection of appropriate fall protection systems. OSH maintains copies of all records for services provided by OSH pertaining to this Program. An OSH Program Coordinator is designated to provide guidance, regulatory interpretation, and oversight for this Program and to review this Program annually.
Deans, Department Heads, and Directors (Campus Units)
Campus Units shall designate a Responsible Person that will be charged with implementing this Program and unit-specific SOPs. Campus unit shall provide the resources necessary to implement this Program and unit-specific SOPs.
Campus Unit Responsible Person (Competent Person)
The Campus Unit Responsible Person shall complete fall protection competent person training and work with OSH to identify fall hazards in their Campus Unit. The Responsible Person shall identify other individuals within the unit to serve as competent persons, as needed, and ensure they receive appropriate training. The Responsible Person shall work with Campus Unit Supervisors to identify personnel that may be exposed to fall hazards and ensure that all personnel within their unit affected by this Program receive proper training. The Responsible Person shall ensure that unit-specific SOPs are reviewed annually.
Supervisors of Affected Employees (Supervisors)
Supervisors and Principle Investigators (PIs) are responsible for enforcing proper work practices and use of fall protection equipment under their responsible charge in accordance with this Program and unit-specific SOPs. They shall assist in the development and annual review of unit-specific SOPs. They shall ensure that all their personnel who may be exposed to fall hazards receive training appropriate to the fall hazards to which they are exposed. They shall furnish appropriate fall protection equipment and devices for their employees exposed to fall hazards.
Employees
Employees shall follow the requirements of this Program, unit-specific SOPs, and training. They shall not perform work at height for which they have not been trained. They shall identify fall hazards prior to beginning work and implement controls to protect from falls. Hazards that the employee cannot control shall be reported to their supervisor.
PROCEDURES
General
Working at height is defined as work on a surface that has an unprotected side, edge, etc. four feet or more above an adjacent lower level; when working from aerial lifts or other elevated work platforms; and when working above dangerous equipment. All employees will be protected from falling when working at height.
Fall hazards will be evaluated by a Campus Unit fall protection competent person with assistance from the Campus Unit Responsible Person and the OSH Program Coordinator upon request to determine the best method to protect the employee. When selecting what type of fall protection to use, the fall protection competent person will consider the hierarchy of hazard controls, which organizes risk control techniques from most- to least-effective.
Program Evaluation
This Program will be reviewed annually by OSH. The written Unit-Specific SOPs shall be reviewed and updated by the respective Campus Unit at least annually and more frequently as hazards, tasks, procedures and/or equipment change.
Appendices:
The following documents provide information on the university’s programs to protect staff, faculty, students, and visitors from lead exposure.
Lead Awareness Training
This class discusses the use of lead compounds in university campus buildings. Topics include the health effects associated with lead exposure, sources and uses of lead materials, types of materials present on the university campus, regulations in effect for lead workplace exposure, and controls in place for the prevention of lead exposure in the work place.
Respirator Training and Fit Testing
Employees must wear respirators to protect themselves from hazardous chemicals and dusts in the air when doing certain tasks. This one hour training program discusses why respirators must be worn, the correct way to wear a respirator, medical requirements and how to properly clean, care for and maintain a respirator. Fit testing involves the respirators available through Central Stores.
For Lead Awareness Training and Respirator Training and Fit Testing, please call 217-265-9828. Information on worker training in lead is available through Illinois Department of Public Health (IDPH) approved trainers.
More information is available at the IDPH website under the topic of lead.
Hand and power tools are a common part of our everyday lives and are present in almost every industry. These tools help us to easily perform tasks that otherwise would be difficult or impossible. However, these simple tools can be hazardous and have the potential for causing severe injuries when used or maintained improperly. Special attention toward hand and power tool safety is necessary to reduce or eliminate these hazards.
Moving machine parts have the potential to cause severe workplace injuries, such as crushed fingers or hands, amputations, burns, or blindness. Safeguards are essential for protecting workers from these preventable injuries. When the operation of a machine or accidental contact injures the operator or others in the vicinity, the hazards must be eliminated or controlled.
Assessment Guide
Each Campus Unit shall conduct machine guarding assessments utilizing these Guidelines, manufacturer instructions, national consensus standards, applicable federal or state regulations, or other appropriate guidance or recommendations. Safeguards must protect the operator and other employees in the machine area from hazards, such as those created by point of operation, in-running nip points, rotating parts, flying chips, and sparks. In addition, they must meet these minimum general requirements:
- Secure: Workers should not be able to easily remove or tamper with the safeguard because a safeguard that can easily be made ineffective is no safeguard at all. Guards and safety devices should be made of durable material that will withstand the conditions of normal use. They must be firmly secured to the machine.
- Protect from falling objects: The safeguard should ensure that no objects can fall into moving parts. A small tool that is dropped into a cycling machine could easily become a projectile that could strike and injure someone.
- Protect from flying chips and sparks: When cutting, shaping, and/or milling various materials, flying chips and/or sparks can be generated. To address this hazard, a combination of physical barriers (fixed or adjustable) and proper personal protective equipment may be needed. Retro-fitting some equipment may also require custom (or fabricated) barriers, such as machining turn-of-the-century equipment that predates machine-guarding regulations and concepts.
- Allow safe lubrication: If possible, one should be able to lubricate the machine without removing the safeguards. Locating oil reservoirs outside the guard with a line leading to the lubrication point will reduce the need for the operator or maintenance worker to enter the hazardous area.
- Create no new hazards: A safeguard defeats its purpose if it creates a hazard of its own, such as a shear point, a jagged edge, or an unfinished surface, which can cause a laceration. The edges of guards, for instance, should be rolled or bolted in such a way that they eliminate sharp edges.
- Create no interference: Any safeguard which impedes a worker from performing the job quickly and comfortably might soon be overridden or disregarded. Proper safeguarding can enhance efficiency since it can relieve the worker’s apprehensions about an injury.
Useful Links:
OSHA 1910 Subpart O Machinery and Machine Guarding
OSHA 1910 Subpart P Hand and Portable Powered Tools and Other Hand-held Equipment
Review the Powered Industrial Truck Program for assistance in providing a safe campus work environment while meeting or exceeding Illinois Department of Labor (IDOL) and Occupational Safety and Health Administration (OSHA) regulations.
PURPOSE
The University of Illinois Urbana-Champaign (U of I), through the Division of Safety and Compliance (S&C), Occupational Safety and Health Department (OSH), has established this Powered Industrial Truck (PIT) Program to assist campus units in providing a safe work environment and to promote compliance with State and Federal occupational safety and health standards, particularly the Powered Industrial Truck Standard of the Occupational Safety and Health Administration (OSHA) located in 29 CFR 1910.178 and enforced by the Illinois Occupational Safety and Health Administration (ILOSHA).
It is expected that campus units will develop written unit-specific standard operating procedures (SOPs) to complement and meet the requirements detailed in this program, including completion and submission of Appendix A to OSH.
RESPONSIBILITIES
Occupational Safety and Health (OSH)
OSH is responsible for the administration of this Program. OSH maintains copies of all records for services provided by OSH pertaining to this Program. An OSH program coordinator is designated to provide guidance, regulatory interpretation and oversight for this Program and to review this Program annually.
Deans, Department Heads, and Directors (Campus Units)
Campus units shall designate a Responsible Person that will be charged with implementing this Program and unit-specific SOPs.
Campus Unit Responsible Person
The Campus Unit Responsible Person shall understand the requirements of this PIT Program and applicable OSHA regulations and shall complete the PIT training. The Responsible Person shall work with campus unit supervisors to identify personnel that operate PITs and ensure that all personnel within their unit affected by this Program receive proper training. The Responsible Person shall ensure that unit-specific SOPs are reviewed annually.
Supervisors of PIT Operators (Supervisors)
Supervisors and Principle Investigators (PIs) shall understand the requirements of this PIT Program and applicable OSHA regulations and shall complete the PIT training. Supervisors are responsible for enforcing proper work practices under their responsible charge in accordance with this Program and unit-specific SOPs. They shall assist in the development and annual review of unit-specific SOPs. They shall ensure that all their personnel who operate PITs receive training and authorization to operate the unit’s PITs.
PIT Operators
Employees shall follow the requirements of this Program, unit-specific SOPs, and training. They shall not operate any PITs for which they have not been trained and authorized. They shall complete the Daily Pre-Use Inspection Checklist before operating any PIT. They shall observe the operation of PITs in their unit and report unsafe practices to their supervisor.
PROCEDURES
Training and Evaluation
Operator training, evaluation and certification shall be conducted by designated personnel who have the knowledge, training and experience to train prospective PIT operators and evaluate their proficiency.
Initial training is the responsibility of the campus unit. Contact OSH for assistance in identifying options for training providers.
Operator Evaluation and Re-evaluation
Prospective PIT operators must complete an operator evaluation before being authorized to operate any PIT. Operator evaluations shall be completed by the campus unit’s responsible person or employee’s supervisor prior to granting authorization to operate a PIT.
Appendix B provides an operator evaluation form that must be completed for each operator for each PIT they are assigned to use, at least every three years. Copies of the completed operator evaluations must be provided to OSH upon request.
Refresher Training
Refresher training is required only under the following circumstances:
- The operator has been observed to operate the vehicle in an unsafe manner;
- The operator has been involved in an accident or near-miss incident;
- The operator has received an evaluation that reveals that the operator is not operating the truck safely;
- The operator is assigned to drive a different type of truck; or
- A condition in the workplace changes in a manner that could affect safe operation of the truck.
Certification
The trainer shall certify that each operator has been trained as described above. The written certification will include the operator’s name, date of training, and identity of person(s) performing the training.
Authorization
The Campus Unit Responsible person or employee’s supervisor shall authorize each PIT operator on the PIT(s) they will operate after successful completion of the training certification and evaluation processes, and prior to work assignments requiring PIT operation. See Appendix B of this document for the authorization form.
Pre-Use Inspection
Prior to the operation of any PIT, the Pre-Shift Inspection Checklist found in Appendix C, or a checklist specific to the model of PIT in use must be completed. This applies at the beginning of every work period, and whenever a new equipment operator takes control of the PIT.
Operation
Only authorized personnel may operate a PIT. Trainees may operate a PIT only under the direct supervision of an authorized PIT operator and where such operation does not endanger the trainee or other personnel.
Program Evaluation
This Program will be reviewed annually by OSH. The written unit-specific SOPs shall be reviewed and updated by the respective Campus Unit Responsible Person, with input from supervisors and operators, at least annually and more frequently as hazards, tasks, procedures and/or equipment change.
Specific equipment information including safe operating procedures, training, maintenance, and inspection should be obtained from the equipment manufacturer’s representatives.
Appendices:
Useful Resources:
OSHA 1910.178 Powered Industrial Trucks